Is your HVAC/R Preventive maintenance program... Preventing anything?
- mechanical78
- Jan 10, 2023
- 4 min read
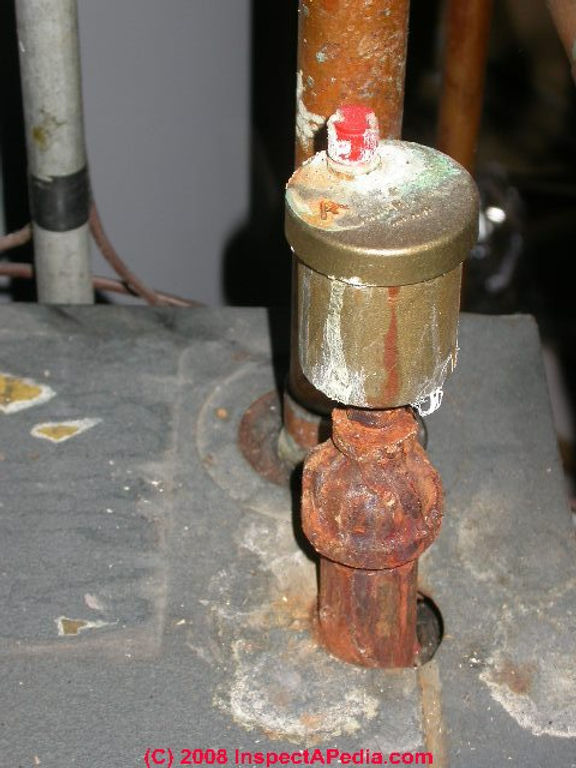
Sure, you've all heard it before. "We are coming to do a PM." (Short for preventive maintenance). The techs show up, spin a few filters, maybe cycle the thermostats or some pumps or fans, and BOOM, you're presented with an invoice that states "Completed PM."
A few weeks or days later, the problem hits you, emergency no heat, no air-conditioning, or a refrigeration unit not holding temperature, and your product is in danger.
I am not at all indicating that some problems do not arise after a PM is done. You cannot tell the future or when a specific component will fail. But pay attention to what problems show up if you have a regularly scheduled preventive maintenance program and ask if they were possibly preventable.
I have been in this trade for decades now, and it is a funny thing. You try to tell a customer the benefits of a PM schedule, and if they don't have a problem now, they do not want to invest. It's understandable. No one wants us when the weather is mild or pleasantly cool. But the weather turns fast, especially here in the Northeast. Just 2 weeks ago we dropped over 40 degrees in less than 8hrs and had a flash freeze. We preach the PM, but are denied a lot as some customers only deal with putting out the fire in front of them at that moment. Then the freeze hits, and you're left waiting for service for an issue that may have been preventable.
For example. I recently received a call from a potential customer in the Princeton area that had some Aerco condensing boilers (PJM has Aerco factory certified techs, and I am also certified myself) and these boilers had some leaks. The leaks weren't on the boiler itself, but on some piping around the boiler. I asked if the boilers have had PM's performed regularly, as Aerco has a recommended 12-month and 24-month PM kit from the factory. The gentleman's response? We aren't having any issues with it right now, just want to get these leaks cleaned up.
Fast forward less than a week later, and as you can imagine, the flash freeze hit. This potential customer calls with an emergency. BOTH his boilers are in fault. He unfortunately has to wait, as our service contract customers get priority. Once a tech arrives, it is found the boiler just needs a PM, which may sound like great news. But the other unfortunate thing, is the Aerco PM kits are 2-3 days away at the factory.
In this particular scenario, this situation is completely avoidable. PJM has propriety audit sheets, and with those audit sheets, if issues are found, usually a proposal will follow up, so you can make a decision if the repair is needed immediately, or if you have time to budget. Our customers have been using these audit sheets to hold us accountable as well. If you received 6 audit sheets in a row, where everything is checked off as "Good", then how could you possibly be told your HVAC unit or boiler is old, inefficient, and now needs to be replaced suddenly? It also helps us, because it is a paper trail to show the issues have been identified and recorded. It is a win-win.
A lot of property and facility managers have enjoyed the use of our equipment rosters and audit sheets to track their HVAC/R assets. We feel we give you a realistic chance to prevent downtime and emergency, along with a "Critical spare parts" list, so you're not waiting those 2 or 3 days (or even more!) for parts. I have seen too many issues like the pictures above, while visiting sites that are under a preventive maintenance program. Sure, they seem harmless. Sure, it's not an issue right now, but they have the potential to turn into emergencies, downtimes, and loss of production. We have had offices close due to these issues, which hits the bottom line hard. This should have been picked up on a PM, noted on the audit sheet, and a proposal presented, so the customer had it in writing, and had the cost to compare to help make a decision.
Do you know what you're paying for? Do you know what the techs do during their "PM"? Do you know if the important components were tested correctly?
Do you know how old your equipment is, and what the life expectancy of that equipment is, so you can plan and budget accordingly? Or do you want to be told one day, your Carrier or Trane rooftop package unit is 20 years old, and parts aren't available, and you need a new one, which, by the way, is 8-12 weeks away and now forcing you to spend thousands to put a band-aid on it, just so you can spend thousands to replace it in 8-12 weeks.
Do you have problems with power or applications that cause compressor or motor failures more often than it should? Maybe there's an unknown humidity issue in your building, or the air handlers gas heat is way too big, causing units to "Short-cycle" and lose heat exchangers prematurely. This could and should all be tracked.
Let PJM build your equipment roster, audit sheets, and a customizable PM plan for your HVAC/R assets and buildings or campus. We serve NJ, Southeastern PA, and Northern Delaware. Call today or email me at dgriffin@Pjmmechanical.com , before the winter really hits. It won't cost you anything to have a conversation, unless you're asking for emergency service due to being reactive, and not proactive!
Dennis Griffin
Comments